Quality Assurance
Our products are mainly purchased by corporate customers as production goods. To obtain our customers' trust that they definitely gain reassurance from buying Fujikura Kasei's products, we have created a quality management system and engage in improving both the quality of our products and the quality of our work as our contribution to society.
Our basic concept of quality assurance
We produce our products always from the customer needs point of view. We have established a quality management system based on ISO9001 standards (Table 1) and engage in quality assurance activities as one across our Group so we may respond promptly and accurately to upgraded customer demand for quality. Furthermore, to provide globally uniform quality across our entire Group, we are promoting the acquisition and/or maintenance of ISO9001 certification by our Group companies in and outside Japan and ensuring continuous improvement by implementing quality maintenance activities.
Quality policy
- We always work on our products with creativity and aim to be number one in customer satisfaction with "Quality and Speed!".
- In order to further strengthen our quality-oriented management, we will strive to improve effectiveness by conforming to the ISO9001 quality management system standard and continuous improvement.
- In order to meet the expectations of our customers, we set quality goals, evaluate the degree of achievement, and carry out quality improvement activities across the company.
- We will communicate the quality policy to all employees, promote understanding and dissemination, and carry out education and enlightenment activities for all employees in order to realize the quality goal.
- In order to maintain the operation of the quality management system in consistency with the quality policy, we regularly review its suitability and carry out necessary reviews.
Fujikura Kasei Co., Ltd.
President
Daisuke Kato
Table 1. Quality management system certification status
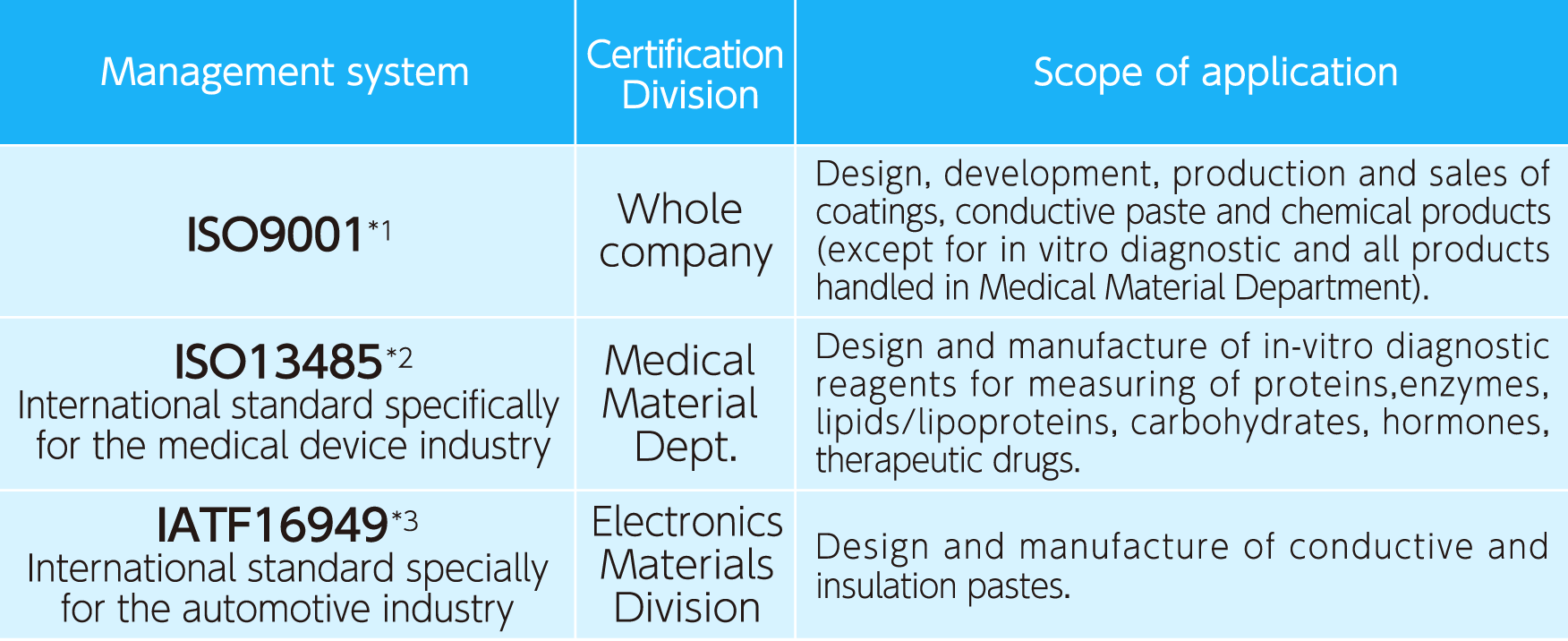
- *1 Japan Management Association Quality Assurance Registration Center (JMAQA)
- *2 SGS Japan Inc.
- *3 LRQA Limited
Table 2. ISO9001 certification status of Group companies in Japan and overseas that have production sites
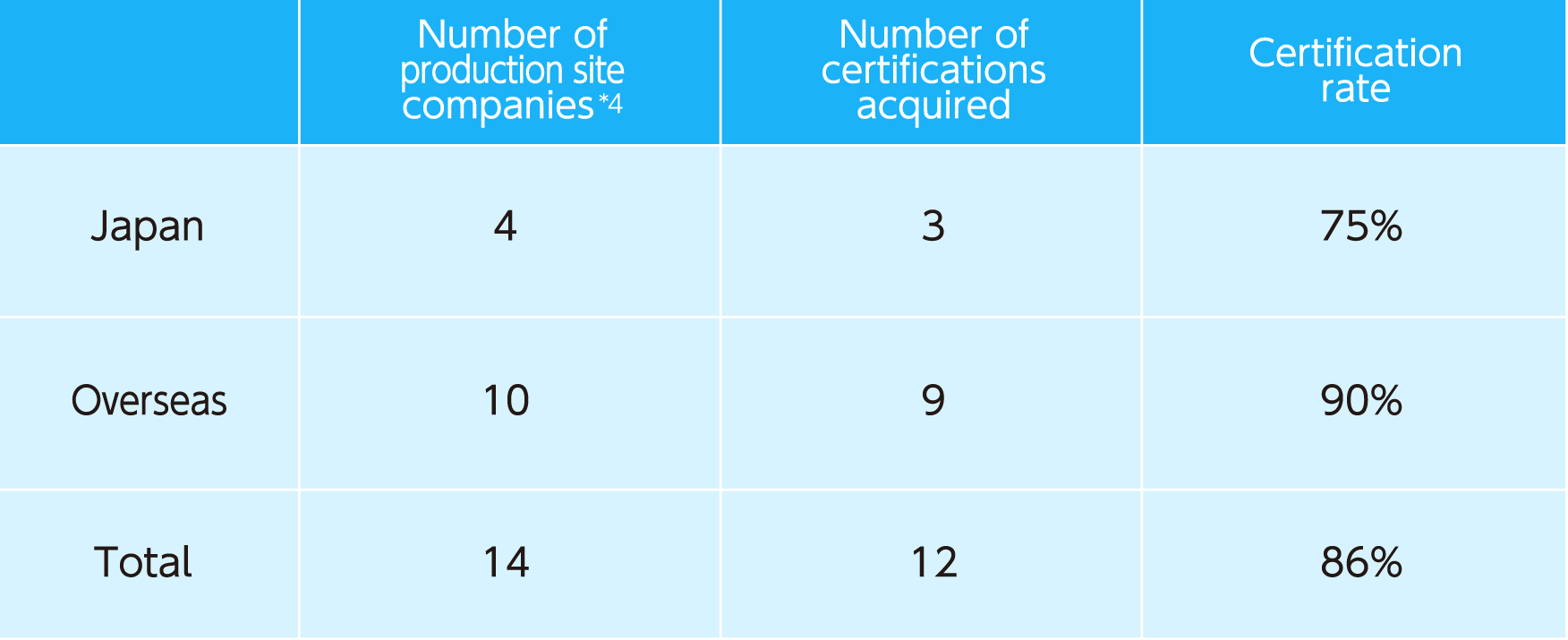
- *4 Companies that have production sites, including Fujikura Kasei
Quality assurance framework
To maintain product quality (including the management of chemicals in products*5), we have a quality assurance framework in place for all processes from the planning, design, manufacture and shipment of products to their use by customers.
In the event of a quality trouble (quality flaw or customer complaint), the Quality Assurance Department, business divisions, and production departments work as one to investigate the cause and take action to prevent recurrence. The Quality Assurance Department has a proper system in place to guarantee quality always from the customer needs point of view, as a separate department directly under the president, independent of other business divisions and the production department.
Additionally, we have established a Quality Assurance Promotion Meeting composed of members from each division and department to pursue activities such as for maintaining and improving our company-wide quality management system and proposing solutions to quality-related issues.
From fiscal 2018, efforts are being made to prevent quality troubles by identifying issues beginning with the design stage of products and strengthening design reviews. With regard to complaints that have been received from customers, however, efforts are being made to prevent similar complaints by strengthening the review and follow-up of measures.
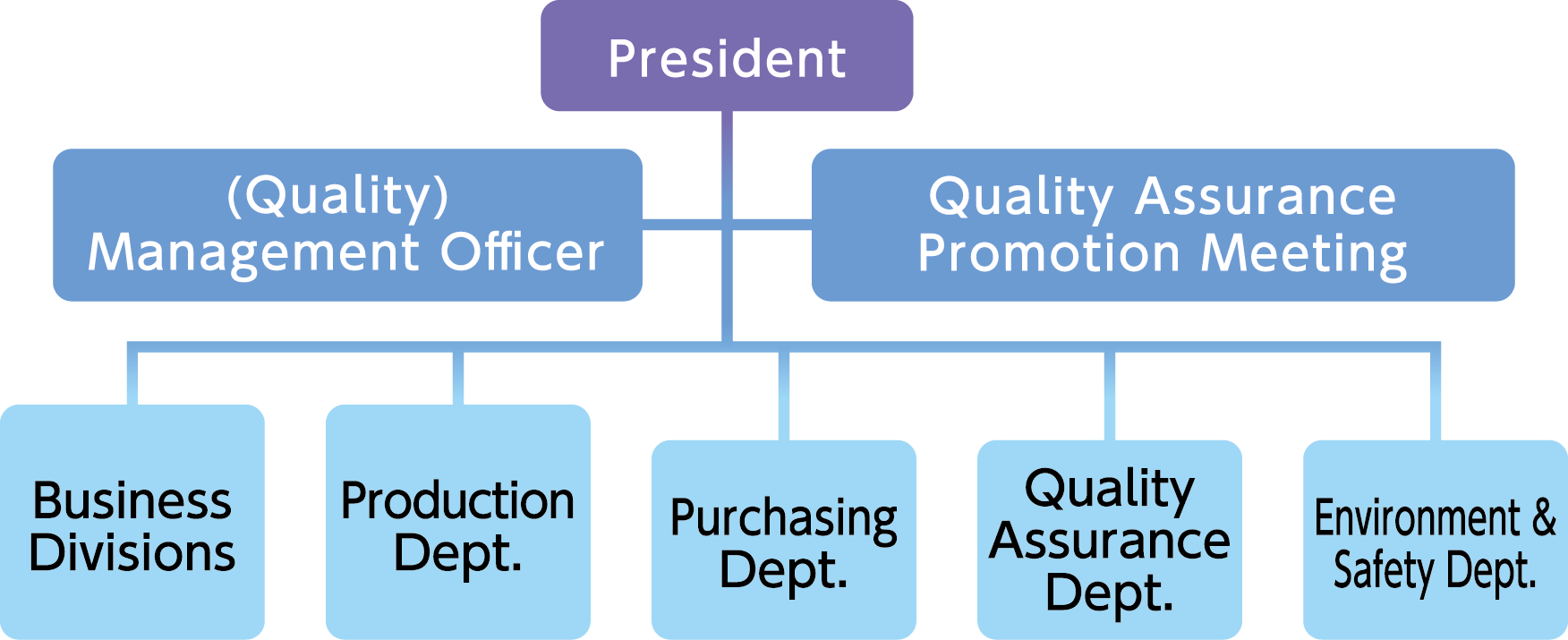
- *5 Details on the management of chemical substances contained in products are provided in the section on chemical substance management.
Medium to long-term initiatives concerning our quality assurance system
At Fujikura Kasei, we have formulated our 11th mid-term management plan with an eye to realizing our 2030 vision. Among the quality activity plans, we will place particular focus on the following.
(1)Initiatives to provide high quality and globally uniform quality by the entire Group
- Implementation of quality control activities in our overseas Group companies (in Vietnam, Malaysia, Indonesia) to unify testing methods and equipment and firmly establish our quality assurance system (China and India to be included in FY2024)
- Introduction of a trend management system for raw materials and products to enhance manufacturing quality and prevent quality troubles (70% rate of introduction)
(2) Initiatives for establishing a sustainable quality assurance system
- Promotion of paperless quality data and documents for efficient information sharing and reduction of labor
- Lateral dissemination of countermeasures and strengthening follow-up efforts to prevent quality troubles and reduce waste
- Promotion of the automatic issuing of inspection results to eliminate inspection fraud